Communication cable manufacturing need to pay attention to what problems? Kexun Cable summarized the following points for everyone:
1. Raw materials, the best use of copper rods for oxygen-free electrical, its resistivity and tensile strength, elongation to meet the standard requirements, insulation materials using HDPE high density polyethylene, insulation volume resistivity to ensure that aluminum plastic composite tape The tensile strength and the thickness of the aluminum layer should comply with the corresponding standards.
2. For wire drawing, for example, HYA 1200*2*0.4 has a conductor diameter of 0.4mm, which is generally drawn using a 280 continuous annealing copper drawing machine. The annealing current, take-up tension, and cable are controlled during drawing. This step is very good. The key is that the 0.4mm copper wire pulled out must ensure that the diameter deviation is within ±0.004mm, and the f-value is less than or equal to 0.004. Otherwise, the resistance will be exceeded and the resistance will be unbalanced.
3. Insulation extrusion, color masterbatch and insulation material are generally prepared at a 1:50 ratio. Insulation extrusion is preferably performed with a laser on-line caliper gauge and an extruder linkage production line to ensure uniform insulation outer diameter, otherwise it will affect Work capacitance, capacitance imbalance and other parameters performance.
4. The core pairs are twisted, subunits and super units are cabled. The twisting pitch should be controlled strictly according to the calculated chromatographic pitches. The chromatographic pitches are based on capacitance, near-end crosstalk, far-end crosstalk, etc. The parameters were determined by differentiation. When sub-units and super-units SZ stranded cables, the insulated strands are evenly distributed on the distribution board, and it is not necessary to save time and effort. To wear many pairs of cores in one branching hole, the stranding tension of the stranded-pair core must be maintained in a moderate size. Uniform, often this part causes the copper wire to be smashed, so that the electrical parameters and other tests are unqualified. In addition, the selection of the color of the chromatogram tie should be strictly performed according to the standard, because the number of large logarithmic communication cables is too many, the ribbon error will be Causes the user to connect incorrectly or reject it.
5. The total cable core is cabled, and the cable diameter ratio, the number of prepared line pairs and chromatography are strictly performed according to the process. If HYAT petroleum jelly filled cable is produced, the pressure of the filling box is generally controlled at 0.4 MPa and the temperature is controlled at 90°C. Filling box mold die aperture should be appropriate, this link should pay attention to the control is not easy to make the core of the cable burned, repair it can be troublesome. In addition, after this process is finished, it is better to conduct the conductor connectivity test and the withstand test of the insulated wire core.
6. Aluminum-plastic bonded LLDPE polyethylene integrated jacket extrusion , this link is often a problem, the width and length of the aluminum-plastic composite tape used in the vertical package should be calculated well, the large-length cable should be ready for the electric iron, magnesium powder to help Flux, used to weld aluminum plastic tape. When the polyethylene jacket is extruded, warm water should be used to cool the jacket. When the jacket is extruded, bubbles on the surface of the jacket can easily adhere to the surface of the jacket. This can cause pitting on the surface of the jacket. This can be solved by adding detergent or detergent to the sink. . Extrusion appearance of polyethylene jacket should be very bright, if there is a matte appearance, you need to raise the temperature of the head, you can also use the gasoline torch to directly blow the head, in order to ensure the appearance. The pressure of the caterpillar when extruding should be adjusted appropriately, otherwise the cable will be flattened.
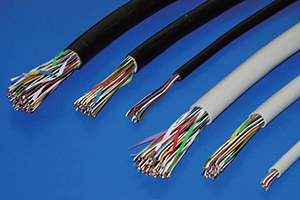
7. Finished product test, large logarithmic communication cable such as HYAT1200*2*0.4 , more than 2400 insulated cores, insulated skin boring head is quite troublesome, often requires 3 or 4 people to use scissors for an hour, suede length is generally 15cm on the line, oil The paste can be filled with the tip in petrol and cleaned. After the insulation boring head has been processed, the parameters and secondary parameters can be checked.
These are the problems that KeXin Cables share for communication cable manufacturing. I hope to be helpful.
Plastic Package High Frequency Welding Machine
Platic package High Frequency Welding Machine
Wide using in environmental protection plastic packing ,toothbrush packing,
environmental production dress-glue products with APET,PETG,GAG materials,
Equally can process any materials needing welding and cutting simultaneously.
double-way automatic slipway, back-forth or continuous delivering the mould,
Accurate-orientation, error±20um.
Adjustable cutting pressure 1-50 ton, stable and reliable in output, firm in structure.
Adopting high sensitive anti-sparkle device NL5557 to avoid damaging the mould efficiency.
Operation mode: oil pneumatic or pure-pneumatic.
Plastic High Frequency PVC Blister Welding Machine has dual shuttles, automatically and enclosed
Plastic Welding Machine,Plastic Package High Frequency Welding Machine,Radio Frequency Plastic Welding Machine,Hf Pvc Welder Machine
Hangzhou Xiaoshan Wanfeng Mechanical & Electrical Equipment Factory , https://www.wanfengmachinery.com